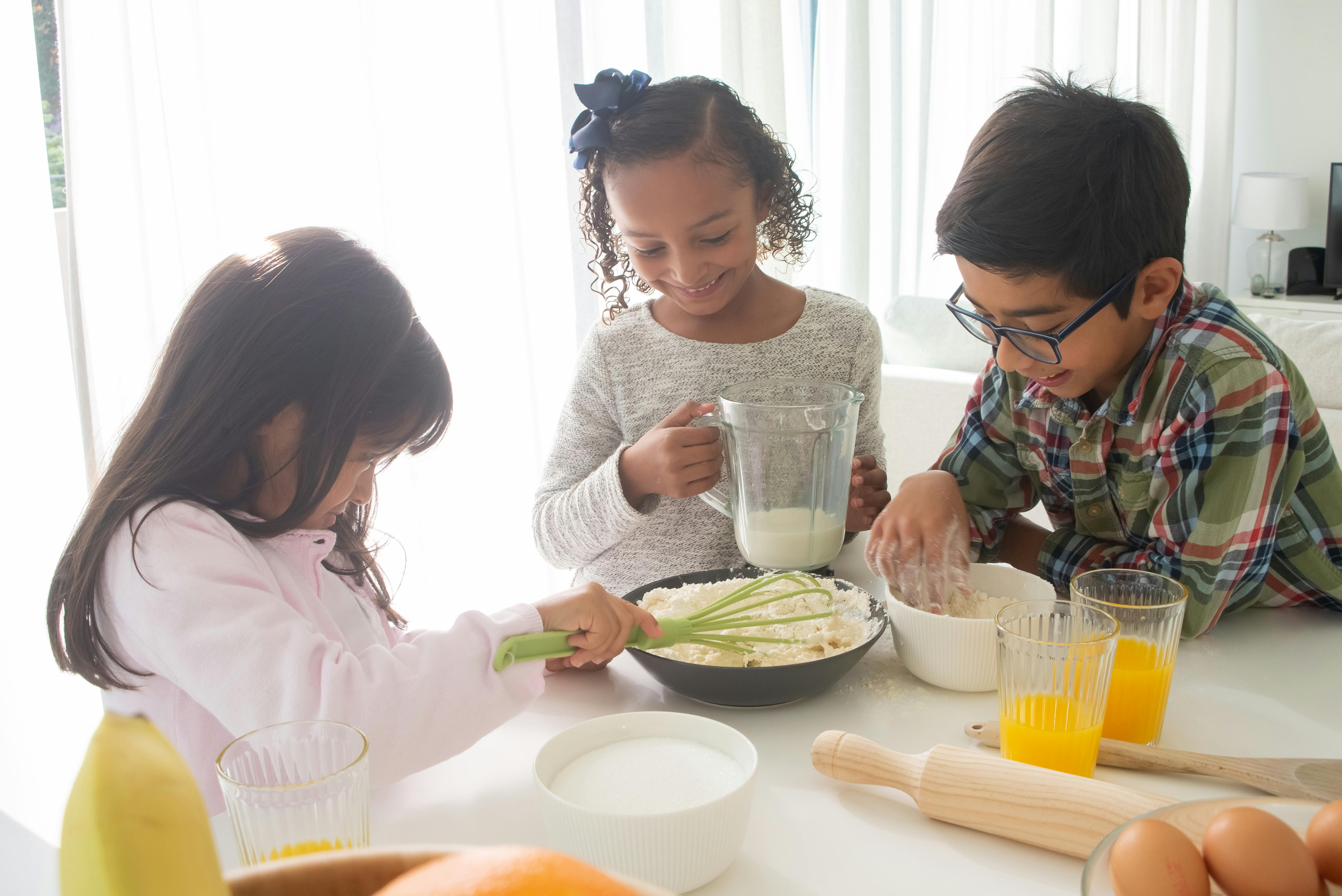
Vacuum metallization: a cost-effective and environmentally friendly alternative to electroplating
If saving the environment and money is on your wish list while plating and coating for your needs, then vacuum metallizing may be your only option. You may want to have a chrome plating and coating to achieve the look, quality, and durability of your products that you want, but you can’t deny the big pocket pinch and the health and environmental hazards associated with it.
The acid used in chrome plating is carcinogenic; It involves the use of cyanide and can cause hydrogen embrittlement. This is a proven solution and an efficiently safe alternative to chrome plating. Vacuum plating equipment is used for a wide range of purposes to make things shine like chrome. From automotive and aeronautical industries to telecommunications industries and various electrical components, this is the safest and most cost-effective solution.
Does vacuum metallization compromise quality and durability?
This process was developed as early as the 1960s and has since evolved and undergone crucial developments in its applications. This process was originally developed for the coating of interior accessories such as dashboards, lights, armrests, etc. Of automobiles. At the time, the process did not involve the application of a top coat, which resulted in rapid erosion of the chrome effect from the exterior, making it vulnerable to scratches.
But now the process has evolved and progressed and those possibilities for susceptibility are almost non-existent. Gives an absolutely shiny metallic finish that can last for years. The progress in this field has been so immense that the top coat can be tinted to produce colored chrome effects and gold imitation effects. However, you cannot get the same durability as a chrome coating and finish, but considering the cost effectiveness and durability it offers, it is quite satisfying.
How is vacuum metallization done?
It is a process where a non-porous substrate such as plastic, metal or glass is used that gives it a simulated chrome finish. A thin layer of pure aluminum evaporates on the surface that requires vacuum coating placed inside an extreme vacuum chamber. Here an aluminum vapor cloud is created and when this cloud comes into contact with the other surfaces, it condenses and adheres to the surfaces to create a uniform thin metallic layer that gives the desired chrome shine effect. Before the metallization operation, the parts to be metallized are bathed and baked to remove the solvents from the base-coat and this ensures a hard and smooth finish to the parts. After the plating process is complete, another protective top coat is applied.
Wide application
Vacuum metallization can have wide applications. The electronics, telecommunications, computer, military, medical, aerospace, automotive, and marine industries involve extensive use of these applications.
This has become a common application now in various industries. Green responsibility and personnel safety are a priority in most industries today, and given the quality and durability of products this process ensures, most industries are choosing this as the safest option. There are many places that deal with this and their vacuum metallizing equipment is top notch. Check the best offers before hiring.